Understanding the Role of Die Cast Mold Manufacturers in Modern Metal Fabrication
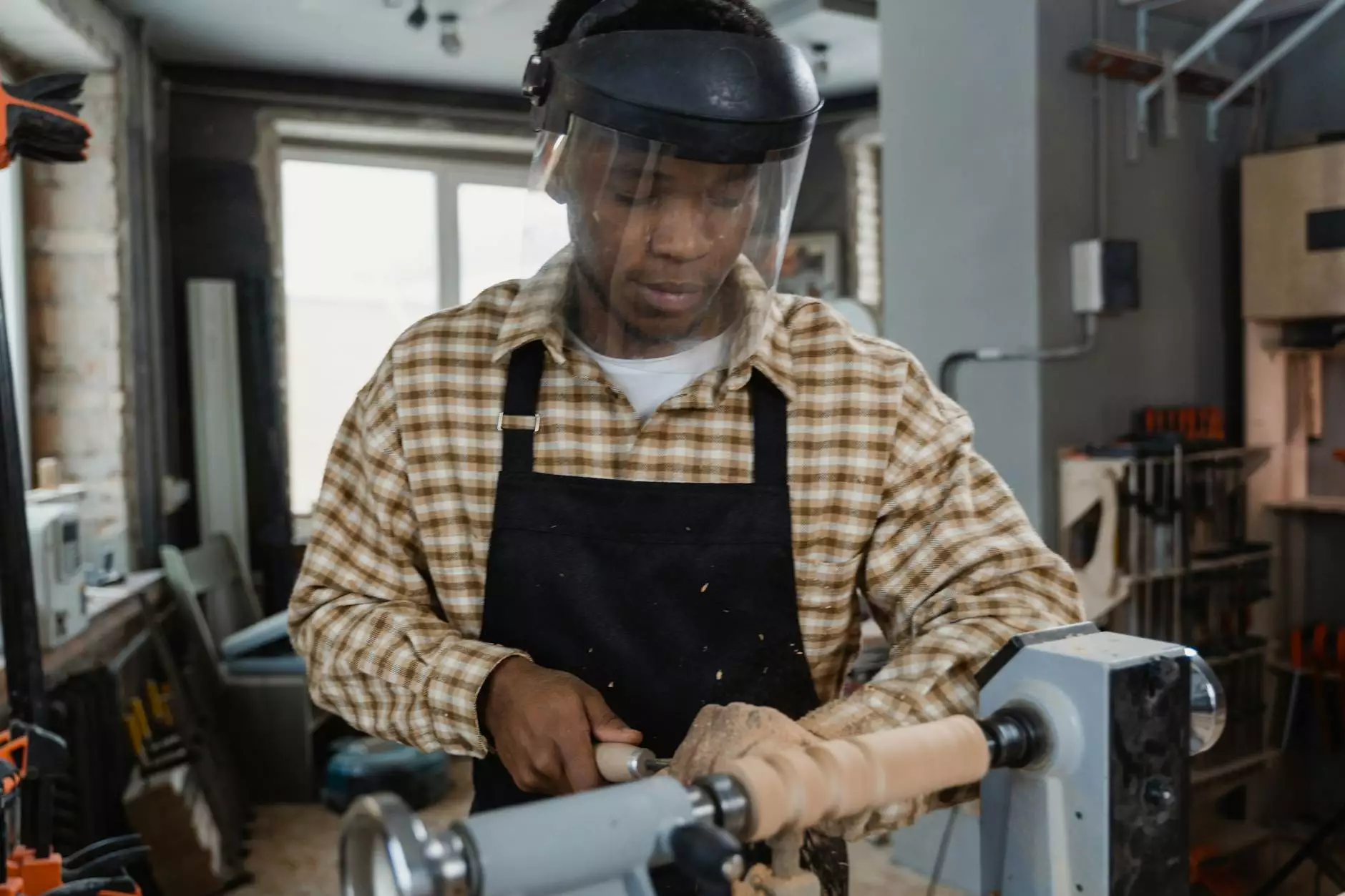
The world of manufacturing is intricately woven with numerous technologies and processes that work in unison to produce the products we use daily. One of the fundamental processes in this vast ecosystem is die casting. At the heart of this process are the die cast mold manufacturers, who play a pivotal role in ensuring that components are produced with precision and efficiency. In this article, we delve deep into the die casting industry, exploring the functions, advantages, and challenges faced by die cast mold manufacturers.
What is Die Casting?
Die casting is a manufacturing process that involves forcing molten metal into a mold cavity under high pressure. This method is widely used for producing complex shapes with a high degree of accuracy. The primary materials used in die casting include aluminum, zinc, magnesium, and copper alloys. The benefits of this process are numerous, including reduced production times, enhanced strength, and excellent surface finishes.
The Importance of Mold Manufacturing in Die Casting
The quality of the mold significantly influences the final product's integrity. This is where die cast mold manufacturers come into play. They are responsible for designing and producing molds that can withstand the rigorous conditions of the die casting process while allowing for efficient production and high-quality outputs.
Key Features of High-Quality Die Cast Molds
- Durability: Molds must withstand extreme temperatures and pressures without deforming.
- Precision: Molds should allow for minuscule tolerances to ensure parts fit seamlessly.
- Complexity: Capable of producing intricate designs that are often impossible to achieve with other manufacturing methods.
- Heat Resistance: Molds need to endure extreme heat levels without losing structural integrity.
Advantages of Using Die Cast Molds
Engaging reputable die cast mold manufacturers comes with several advantages:
1. Cost Efficiency
Although the initial investment for high-quality molds can be significant, the efficiency gained through rapid production often leads to lower per-unit costs. This is especially beneficial for high-volume production runs.
2. Superior Surface Finish
Molds created by skilled manufacturers yield products with excellent surface finishes, reducing the need for post-processing and thereby saving time and money.
3. Consistency in Quality
With precise molds, each part produced is consistent, ensuring that manufacturers can maintain quality standards over large batches.
4. Versatility
Die cast mold manufacturers are equipped to handle a variety of metals and designs, allowing industries to produce a wide range of products, from automotive components to consumer electronics.
Challenges Faced by Die Cast Mold Manufacturers
Despite the benefits, die cast mold manufacturers face a set of challenges that can affect their operations.
1. Technological Advancements
The industry is continually evolving with advancements in materials and technology. Manufacturers must stay updated to remain competitive and meet market demands.
2. Resource Management
The procurement of quality raw materials is essential for producing top-notch molds. Fluctuations in metal prices can impact production costs.
3. Skilled Labor Shortage
As the demand for quality molds increases, the industry grapples with a shortage of skilled professionals who can operate advanced machinery and manage the complexities of mold design.
Trends Shaping the Future of Die Casting
The die casting industry is witnessing various trends that are shaping the future of mold manufacturing:
1. Increased Use of Automation
Many die cast mold manufacturers are adopting automated systems for enhanced efficiency. Automation reduces human error and increases production speed.
2. Emphasis on Sustainability
As industries pivot towards sustainable practices, there is a growing demand for molds that are not only efficient but also environmentally friendly. Manufacturers are exploring recycled materials and energy-efficient processes.
3. Integration of Smart Technology
Smart technologies such as IoT (Internet of Things) are making their way into manufacturing processes. This allows for real-time monitoring and predictive maintenance, enhancing operational efficiency.
Choosing the Right Die Cast Mold Manufacturer
When it comes to selecting a die cast mold manufacturer, various factors need consideration:
1. Experience and Reputation
Look for manufacturers with a proven track record. Experience often correlates with reliability and quality.
2. Quality Assurance Practices
Inquire about their quality assurance processes. Top manufacturers implement rigorous testing and quality control measures.
3. Technical Capabilities
Evaluate their ability to handle specific materials and complex designs relevant to your industry needs.
4. Communication and Support
Effective collaboration can streamline the mold development process. A manufacturer who prioritizes communication can yield better results.
The Impact of Die Cast Mold Manufacturers on Various Industries
Die casting technology is essential across numerous sectors:
1. Automotive Industry
The automotive sector is one of the largest consumers of die cast products. Components such as engine blocks, transmission housings, and structural parts are produced using die casting methods.
2. Consumer Electronics
Die cast molds are pivotal in manufacturing parts for consumer electronics, aiding in producing lightweight and durable items like housings for phones and laptops.
3. Aerospace
The aerospace industry demands the highest levels of precision and durability. Die cast mold manufacturers play a crucial role in producing components for aircraft and spacecraft.
4. Medical Devices
With the rise of advanced medical technologies, die casting is increasingly used in manufacturing reliable and high-precision medical devices.
Conclusion
In conclusion, die cast mold manufacturers represent the backbone of the die casting process and, by extension, the manufacturing industry at large. Their expertise in creating durable, precise, and efficient molds is critical in providing high-quality products across numerous sectors. As technology continues to advance, those involved in die casting will undoubtedly find new methods and innovations to enhance their operations further.
For more insights on die casting and to explore how our capabilities can meet your manufacturing needs, visit us at Deep Mould.